Wear-resistant nylon!
In our daily life, there are many kinds of nylon materials, such as reinforced nylon, wear-resistant nylon, toughened nylon, flame retardant nylon, etc. Each material has its own unique purpose. In actual use, we must choose the right nylon product according to our own needs, and the most suitable product for ourselves. The following is a brief introduction of wear-resistant nylon and high temperature resistant nylon materials:
nylon wear-resistant materials mainly by adding carbon fiber, molybdenum disulfide, graphite, tetrafluoroethylene powder or silicone powder and other materials to reduce the coefficient of friction or wear. Generally speaking, wear-resistant nylon is mainly used in the field of mechanical parts. In recent years, wear-resistant nylon has been widely used in the automotive field.
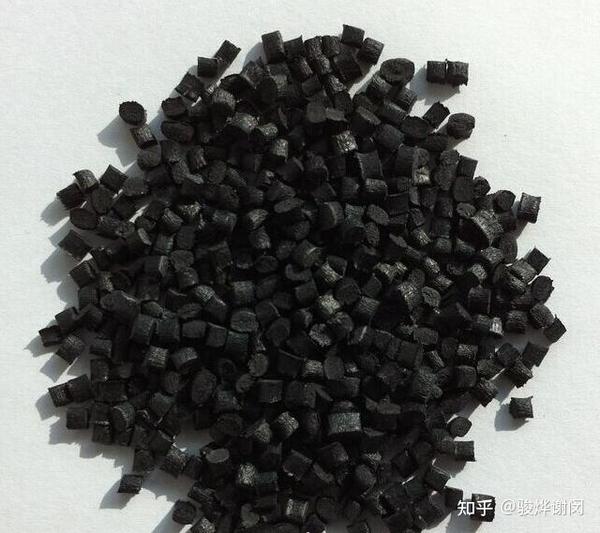
In this application field, domestic companies are also in a leading position in the field of automotive differential gear gaskets, realizing plastic instead of steel. The product has high wear resistance, impact toughness, dimensional stability and good fluidity. Due to price issues, wear-resistant nylon materials have become the preferred material selection target for this application.
However, since the gasket used for the transmission gear has high requirements for accuracy in the thickness direction, strict requirements are imposed on the uniformity of the nylon material in the thickness direction. Traditional wear-resistant nylon products are prone to have a concave effect on the end face due to thermal shrinkage and other factors. In particular, the large size difference between the core shrinkage and the edge shrinkage of the thick piece is a prominent problem, and it can only be used after targeted improvements. This is also the difficulty of technical realization, that is, how to improve the dimensional accuracy of the product on the basis of ensuring the wear-resistant effect, and the cost is not too high.
wear resistant nylon:
wear-resistant nylon is a nylon 1010 resin as the base material, adding a variety of anti-friction materials in the extruder made of nylon 1010 modified plastics. Compared with pure nylon 1010 resin, it has lower friction coefficient, higher PV value, better friction and wear resistance and better self-lubrication. It is suitable for manufacturing various wear-resistant products (injection molding method), such as bearing cage, shaft sleeve, anti-friction ring, anti-friction pad, etc. Commonly used antifriction materials (additives) include graphite, molybdenum disulfide, polytetrafluoroethylene powder, silicone oil, etc. The dosage is generally between 3% and 15%.
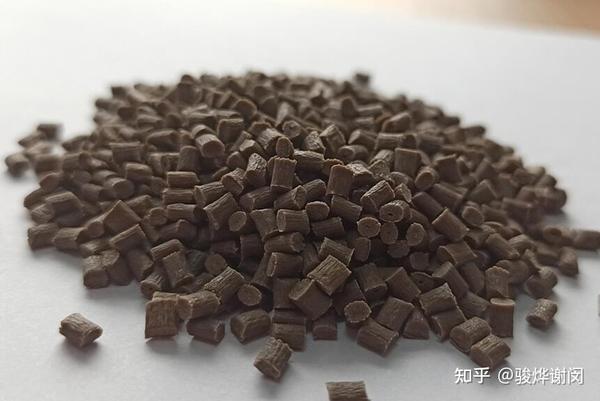
wear resistant nylon:
wear-resistant nylon is a kind of self-lubricating super wear-resistant nylon. This nylon is a good electrical insulator and will not affect the insulation performance due to moisture like other polyamides. Wear resistant nylon has good abrasion resistance, heat resistance, oil resistance and chemical resistance. It also greatly reduces the water absorption and shrinkage of raw materials. It has excellent dimensional stability and mechanical strength.
Super wear-resistant nylon PA66 and PA1010 have good impact resistance, wear resistance, mechanical and chemical stability. Self-lubricating wear-resistant nylon has many improved varieties in plasticization and wear resistance, such as graphite nylon PA12, graphite nylon PA66, graphite nylon PA12, carbon fiber nylon, nylon/molybdenum disulfide alloy, nylon/polytetrafluoroethylene alloy and nylon 1010/molybdenum disulfide alloy. Graphite nylon is particularly suitable for wear-resistant lubricating materials: Graphite is often used as a lubricant in the mechanical industry. Lubricating oil cannot be used at high speed, high temperature and high pressure, while graphite wear-resistant materials can slide at high speed of 200~2000 ℃ and work without lubricating oil. Graphite materials are widely used in many equipment for conveying corrosive media, such as piston cups, sealing rings and bearings. No need to add lubricating oil during operation. Graphite emulsion is also a good lubricant for many metal processing (drawing and drawing pipes). These materials have higher melting points and densities, lower moisture regain and good dimensional stability compared to flame retardant nylons.
Self-lubricating wear-resistant polyamide or tetrafluoro nylon 1010 nylon alloy has high mechanical properties, low friction coefficient, good wear resistance and dimensional stability. It can be widely used in large friction and wear structures used in different environments, such as sliding mechanisms, bushings, oil field equipment, cylindrical bearings, spherical bearings, mechanical cams, gears and other mechanical connectors.